Checking Out the Perks of a Chemical Defoamer in Manufacturing and Manufacturing
The combination of chemical defoamers in production and production procedures provides a strategic advantage by addressing one of the relentless difficulties in commercial operations: foam control. Chemical Defoamer. Comprehending the subtleties of numerous sorts of defoamers and their certain applications can reveal their considerable influence on operational effectiveness and item high quality. As suppliers strive to enhance procedures and enhance customer contentment, the function of chemical defoamers comes to be progressively important. The inquiry remains: how do these materials fundamentally modify the landscape of production effectiveness and cost-effectiveness?
Relevance of Foam Control
While the visibility of foam in making procedures can sometimes seem harmless, effective foam control is vital for optimizing operational performance and product quality. Foam can conflict with numerous phases of production, bring about ineffectiveness that may enhance prices and prolong processing times. In industries such as food and beverage, pharmaceuticals, and chemicals, unrestrained foam can block devices, disrupt automated systems, and ultimately cause item variances.
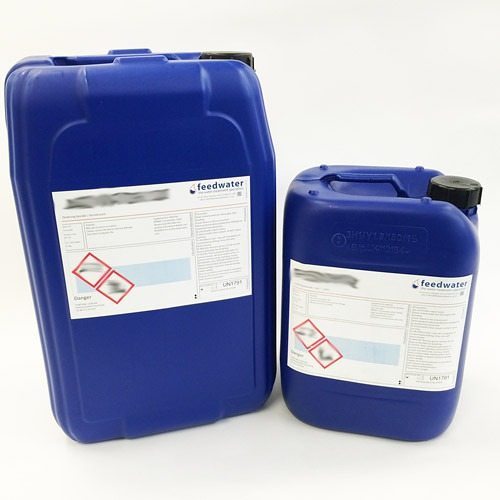
Executing efficient foam control techniques not only boosts efficiency however also supports regulatory compliance in sectors where foam can bring about ecological concerns. By utilizing chemical defoamers, producers can mitigate these challenges, making certain smoother procedures and higher-quality final product. Eventually, focusing on foam control is an essential facet of production that can generate significant advantages in terms of efficiency, safety and security, and item integrity.
Kinds of Chemical Defoamers
What types of chemical defoamers are available for manufacturing processes, and how do they vary in application? Chemical defoamers can be categorized into 3 main types: silicone-based, natural, and not natural defoamers. - Chemical Defoamer

Organic defoamers, usually obtained from natural oils or fats, are efficient in a range of applications, consisting of food and drink production. They are usually chosen for their lower toxicity and environmental influence, making certain compliance with sector regulations.
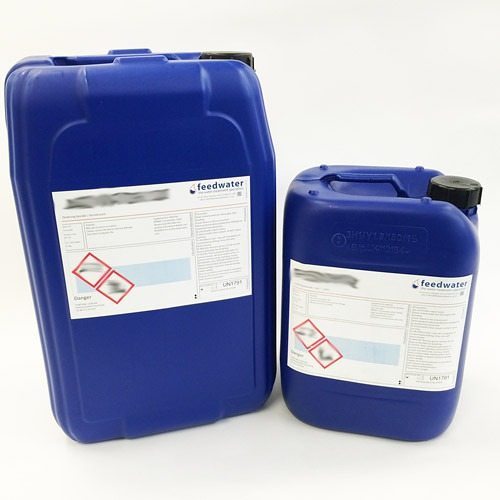
Each type of defoamer serves unique objectives based upon the chemical composition and the particular requirements of the manufacturing procedure, permitting producers to pick the most appropriate choice for their certain needs.
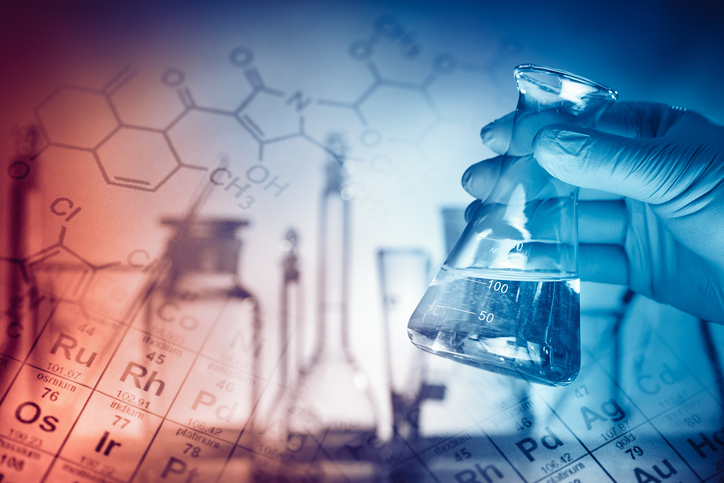
Advantages in Manufacturing Performance
Chemical defoamers play a crucial duty in read more boosting producing efficiency by effectively managing foam generation during different processes. Foam can impede production rates, interrupt tools procedure, and bring about costly downtime. By integrating chemical defoamers, manufacturers can alleviate these problems, making sure smoother operations and increased general productivity.
The usage of chemical defoamers assists maximize the functional performance of equipment such as activators, mixers, and pumps. With minimized foam, these machines can operate at their planned capacity, decreasing the risk of overflow and allowing consistent processing. This results in much better source utilization and higher throughput.
Additionally, chemical defoamers promote faster processing times by decreasing the time required for Continued foam elimination. This acceleration can dramatically impact production schedules, allowing producers to satisfy customer demand much more properly. Additionally, the usage of defoamers adds to decrease power usage, as machinery operates more efficiently with lowered foam disturbance.
Influence On Product Quality
Foam control is not just important for keeping efficiency in making procedures yet also plays a significant function in making sure item high quality. Excessive foam can present air into formulations, leading to variances in the last product. This can materialize as issues such as gaps, uneven textures, or below average finishes, which undermine the designated top quality and performance of the item.
Furthermore, foam can impede the homogeneity of mixtures, resulting in irregular circulation of active components. In markets such as coatings, cosmetics, and food production, this can lead to variants in color, preference, and overall effectiveness. By utilizing a chemical defoamer, suppliers can reduce these threats, making sure that products meet stringent top quality requirements.
Furthermore, regulating foam can enhance the security of emulsions and suspensions, which is essential for ensuring shelf-life and customer contentment. With boosted product consistency and reduced defects, manufacturers can attain greater requirements of quality control, eventually resulting in raised client trust and brand commitment.
Cost-Effectiveness and ROI
Reliable foam control not just boosts item top quality however additionally adds substantially to the total cost-effectiveness of manufacturing procedures. Using chemical defoamers reduces foam-related concerns, which can or else result in production delays, devices malfunctions, and boosted energy usage. By lowering foam, producers can maximize their procedures, causing greater throughput and efficiency.
Spending in chemical defoamers can generate a substantial roi (ROI) The preliminary prices connected with these ingredients are typically offset by the cost savings realized from decreased downtime and enhanced product return. Moreover, boosted item quality can decrease waste and revamp prices, even more strengthening monetary efficiency.
On top of that, efficient foam control can result in minimized water and energy usage, adding to reduced operational prices. This is especially essential in markets where resource efficiency is vital. By incorporating chemical defoamers into their processes, makers can achieve long-lasting financial savings while maintaining affordable rates in the marketplace.
Conclusion
In conclusion, the combination of chemical defoamers in manufacturing and production procedures is necessary for optimizing functional effectiveness and improving product top quality. Effective foam control adds to improved tools efficiency, lowered processing times, and decreased downtime, eventually resulting in considerable cost financial savings. In addition, constant item formulations foster customer fulfillment and brand name commitment. The advantages used by chemical defoamers not only sustain regulative conformity yet likewise give a competitive side in the manufacturing landscape.
The integration of chemical defoamers in manufacturing and manufacturing processes uses a strategic benefit by addressing one of the persistent difficulties in commercial procedures: foam control.While the visibility of foam in producing procedures can sometimes seem safe, reliable foam control is crucial for maximizing functional performance and item quality.Chemical defoamers play an essential duty in boosting producing performance by properly controlling foam generation throughout numerous processes.In addition, chemical defoamers assist in faster handling times by reducing the time needed for foam removal. Furthermore, the use of defoamers adds to reduce energy consumption, as equipment runs much more efficiently with lowered foam check my blog interference.